In the OEM pickleball supply chain, paddle manufacturing often receives the most attention. However, Pickleball Ball Manufacturing presents its own set of technical challenges that directly impact product performance, durability, and production cost. Understanding the key differences between manufacturing methods allows OEM buyers to make informed decisions when sourcing balls for different markets.
1. Two Main Manufacturing Methods
In Pickleball Ball Manufacturing, two core production methods dominate the industry:
- Injection Molding
- Rotational Molding
Each Pickleball Ball Manufacturing method has specific production advantages and limitations that directly affect product durability and playability.
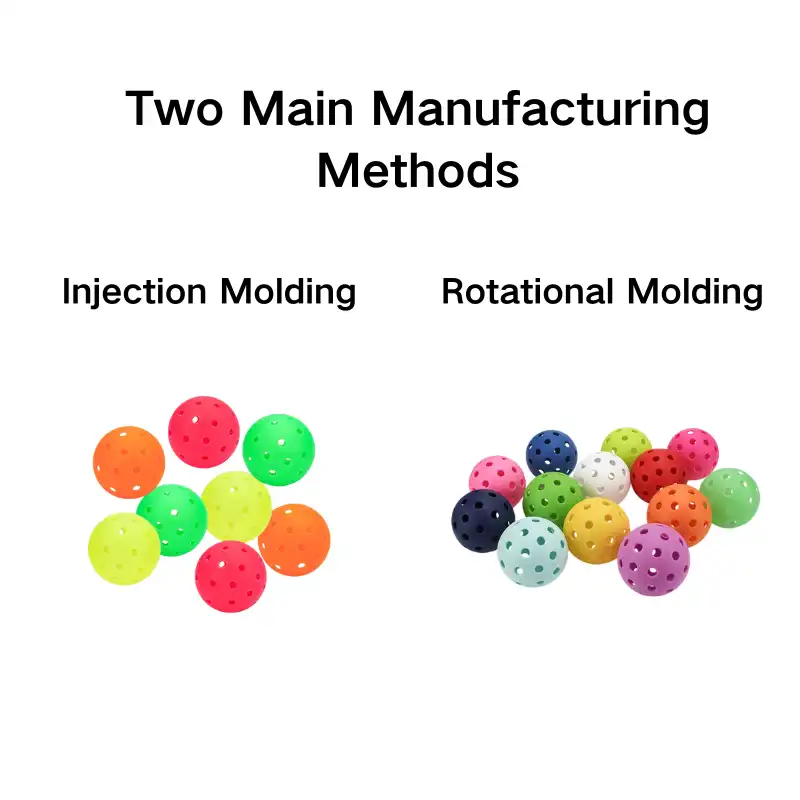
Two Main Manufacturing Methods
Injection Molding: High-Speed Production for Recreational and Training Balls
Injection molding involves injecting melted thermoplastic material (commonly PE or PP resin) into a multi-cavity metal mold under high pressure. The balls are typically formed in two separate halves, which are later bonded together.
Key features:
- Very consistent ball shape and weight
- High production efficiency and lower per-unit cost
- Suitable for both indoor and outdoor pickleball balls
- Widely used for recreational, training, and entry-level competition balls
- Slightly softer surface; may have visible seam line
- Limited wall thickness control for long-term extreme durability
Thanks to its high-speed cycle times and stable output, injection molding is often the default choice for mass-market pickleball balls aimed at casual players and training environments.
Rotational Molding: Premium Durability for Competitive Balls
Rotational molding (rotomolding) involves placing resin powder into a hollow mold, which is then heated and rotated on multiple axes. The powder melts and evenly coats the interior of the mold, creating a seamless one-piece structure.
Key features:
- Seamless, one-piece construction with no weak joints
- Highly durable, resisting cracks and deformation
- Suitable for both indoor and outdoor pickleball balls
- Preferred for tournament-level competitive balls
- Longer cycle time and higher production cost per unit
- Requires precise heat and rotational speed control for wall thickness uniformity
For OEM buyers targeting professional players or premium-level markets, rotational molding offers superior long-term performance, especially under frequent, high-impact gameplay.
This pickleball ball manufacturing choice becomes especially important when differentiating between indoor and outdoor pickleball balls, where bounce behavior, temperature stability, and material resilience vary significantly across playing environments.
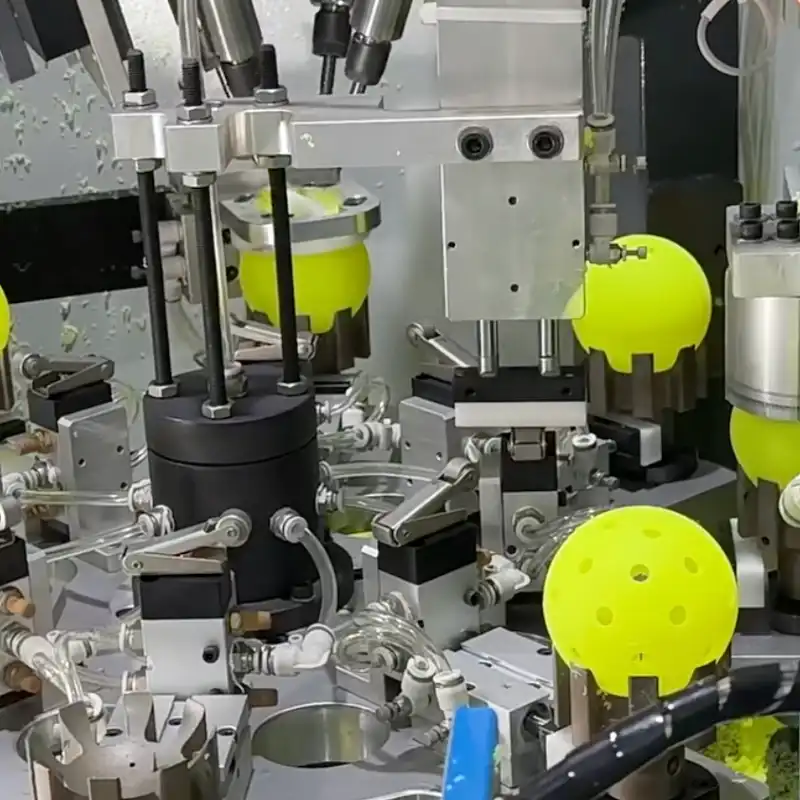
Pickleball Ball Manufacturing
2. Customization Options for OEM Orders
In Pickleball Ball Manufacturing, customization plays a significant role in building brand identity, product differentiation, and expanding OEM production capabilities. OEM factories can typically offer:
- Custom colors: full-color resin blending during material preparation
- Logo printing: pad printing or laser marking, depending on the material surface
- Packaging options: bulk cartons, retail packaging, poly bags, or custom display boxes
- Hole pattern design: adjusting hole count and diameter to modify flight characteristics (usually regulated by tournament standards)
It’s important for buyers to clarify customization needs early during production planning, as some options (such as colored resin) require material pre-mixing before molding.
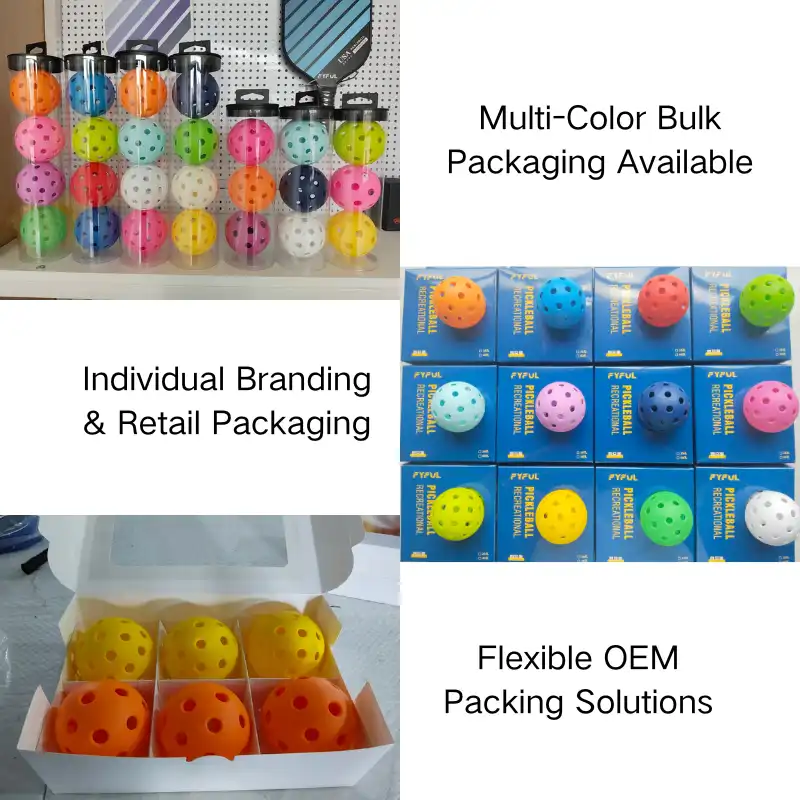
Customization Options for OEM Orders
3. Quality Control in Pickleball Ball Manufacturing
Regardless of the molding method, consistent quality control is essential throughout the Pickleball Ball Manufacturing process. Key QC checkpoints include:
- Ball weight tolerance
- Diameter and roundness uniformity
- Wall thickness consistency
- Surface smoothness and hole edge quality
- Bounce performance testing (drop tests)
For tournament-level balls, maintaining consistent bounce behavior under different temperatures and humidity levels is critical to avoid player complaints and high return rates. Careful control during Pickleball Ball Manufacturing ensures that these performance standards are consistently met.
Summary for OEM Buyers
Understanding the key steps in Pickleball Ball Manufacturing helps OEM buyers align production choices with their target markets and quality standards. Injection molding offers high-speed, lower-cost solutions for entry-level and indoor markets, while rotational molding provides premium durability for demanding outdoor play.
Customization options such as color selection, logo printing, hole design, and packaging give brands flexibility to meet diverse market needs. Careful attention to manufacturing details and consistent quality control ensures product stability, reduces customer complaints, and strengthens long-term brand trust.