In OEM pickleball paddle production, many procurement teams focus on materials, cores, certifications, and graphics. However, one critical factor that directly influences product performance, durability, and appearance is the surface coating of the Pickleball Paddle. Understanding this finishing step is essential for buyers making technical decisions about paddle specifications.
1. Where Surface Coating Fits into the Manufacturing Process
Modern pickleball paddles are typically decorated using UV printing, which applies custom logos and full-color graphics directly to the paddle face.
After UV printing, manufacturers apply a surface coating layer. This layer consists of clear coat spray paint combined with fine matte texture particles. The clear coat spray paint provides a transparent protective seal, while the added texture particles (such as silica or micro-sand powder) create the necessary surface roughness for enhanced spin control.
This two-component coating not only protects the printed graphics but also directly influences the paddle’s playability.
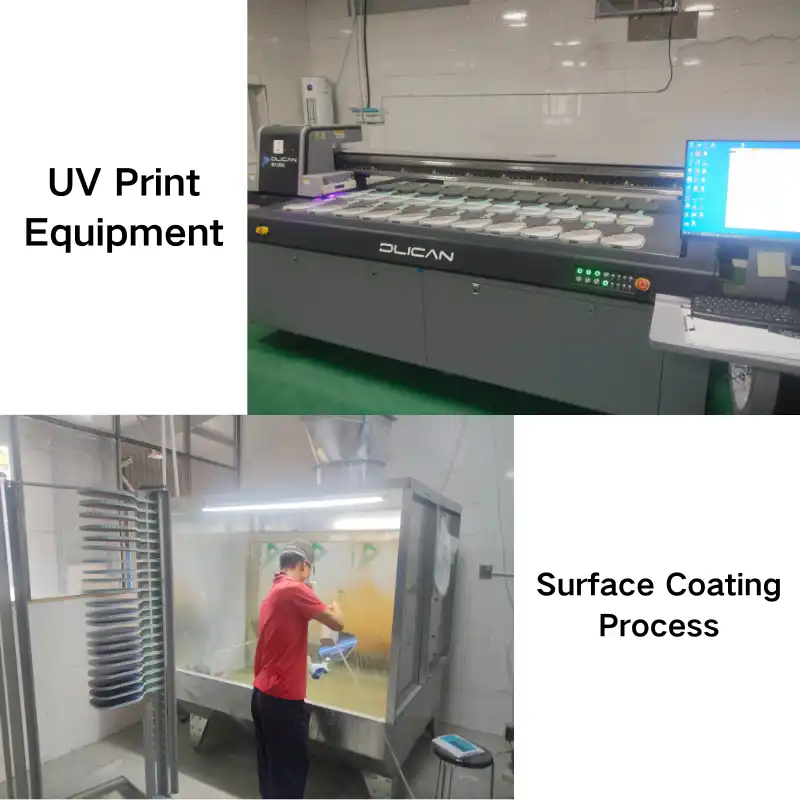
UV Print and Surface Coating Process
2. Surface Texture: Spin Control and Tactile Difference
While the visual appearance of coated and uncoated paddles may seem quite similar, the surface coating creates a clear tactile difference. The micro-texture particles embedded within the coating layer produce a fine, grainy texture that can be easily felt by hand. This added surface friction enhances ball grip during contact, allowing players to generate more spin and better control of shot placement.
In contrast, uncoated paddles feel much smoother to the touch. The raw carbon fiber or fiberglass face provides minimal natural texture, resulting in lower friction and reduced spin potential. For brands targeting performance-oriented players, this controlled surface roughness is often a key design feature that influences buying decisions.
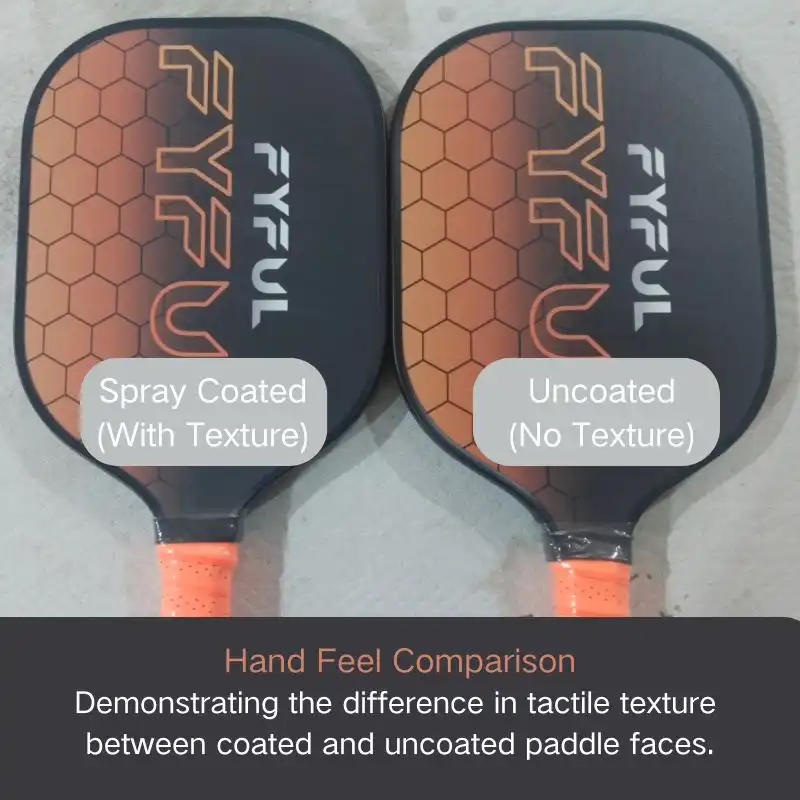
Surface Coating Comparison
3. Durability: Protecting Graphics and Surface Integrity
Beyond playability, surface coating also serves as a durable protective barrier for the UV-printed graphics. Continuous ball impact, moisture, UV exposure, and abrasion from the paddle bag can cause printed surfaces to fade or scratch over time.
The clear coat spray paint component absorbs minor surface wear, while the embedded texture particles maintain consistent friction even after extended use. Over long periods of play, heavy usage may still gradually wear down the coating layer, but the printed design remains protected much longer compared to uncoated surfaces.
Proper care also helps extend the lifespan of coated paddles
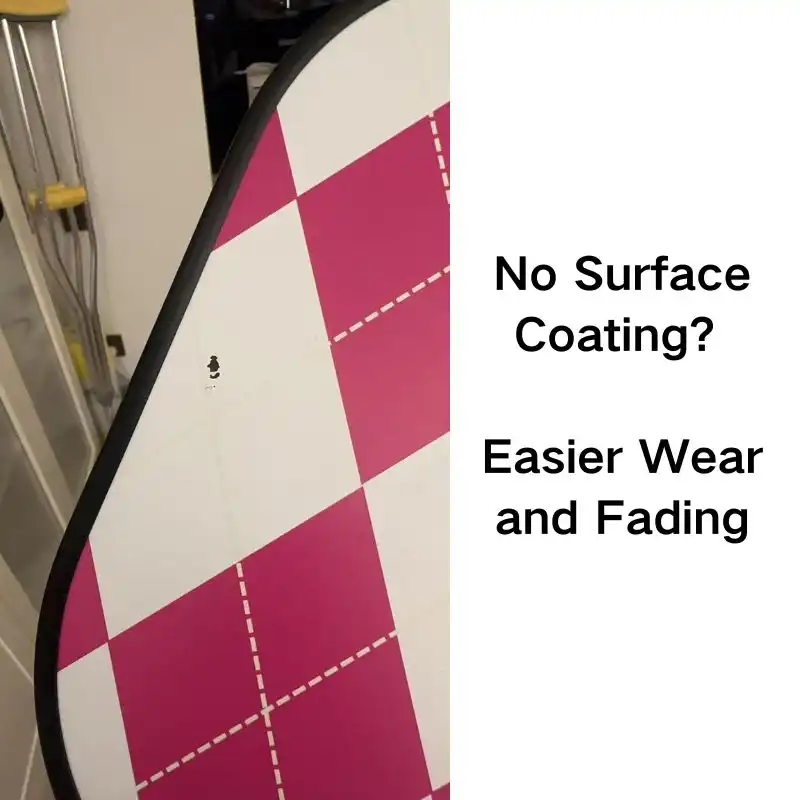
Easier Wear and Fading
4. Visual Consistency: Maintaining Aesthetic Quality
In high-volume OEM production, surface coating helps maintain batch-to-batch consistency. The clear coating smooths out minor imperfections from printing or material variation, delivering a uniform matte or semi-gloss finish.
Without coating, exposed carbon fiber or fiberglass weaves may present natural inconsistencies in color depth or fiber alignment. While some premium brands promote the “raw material” look, most buyers prefer the visually stable appearance that surface coating provides.
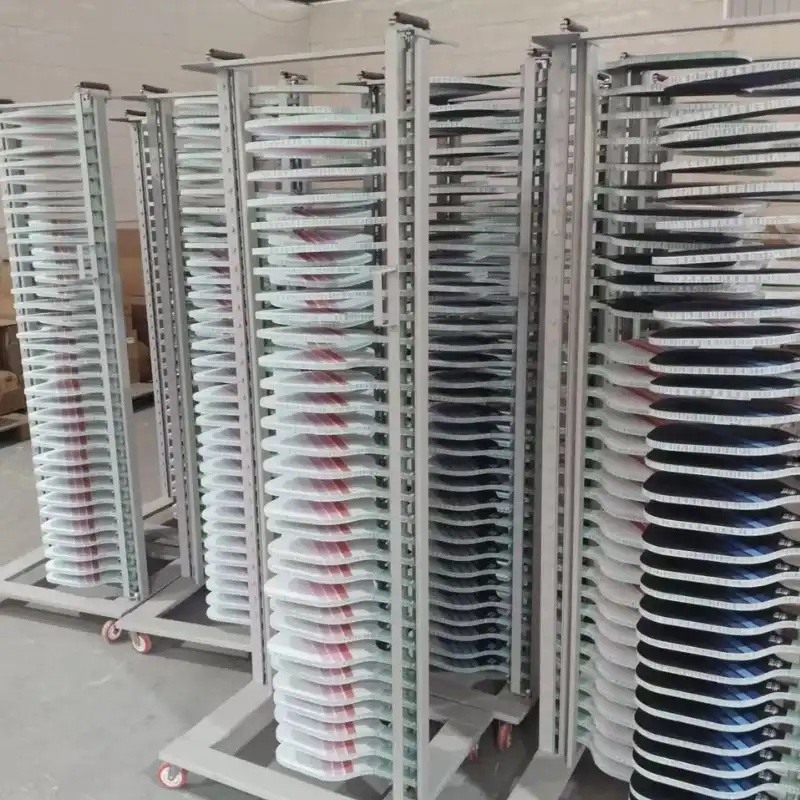
Visual Consistency
5. Cost and Thermal Processing Time Considerations
Adding a surface coating step involves extra labor, materials, and multiple controlled processes. After the clear coat spray paint, combined with fine texture additives (such as silica or micro-sand powder) is applied, the paddles enter a thermal curing stage. This heat processing step ensures the coating fully bonds with the printed surface, locks in the texture particles, and stabilizes long-term durability.
The thermal curing typically takes at least 6 hours under controlled temperature conditions. Including spray application, drying, curing, and final quality checks, this entire process may extend production lead time by 1 to 2 working days for larger orders.
The added production cost generally ranges from USD 0.30 to 0.50 per paddle, depending on order volume and coating complexity.
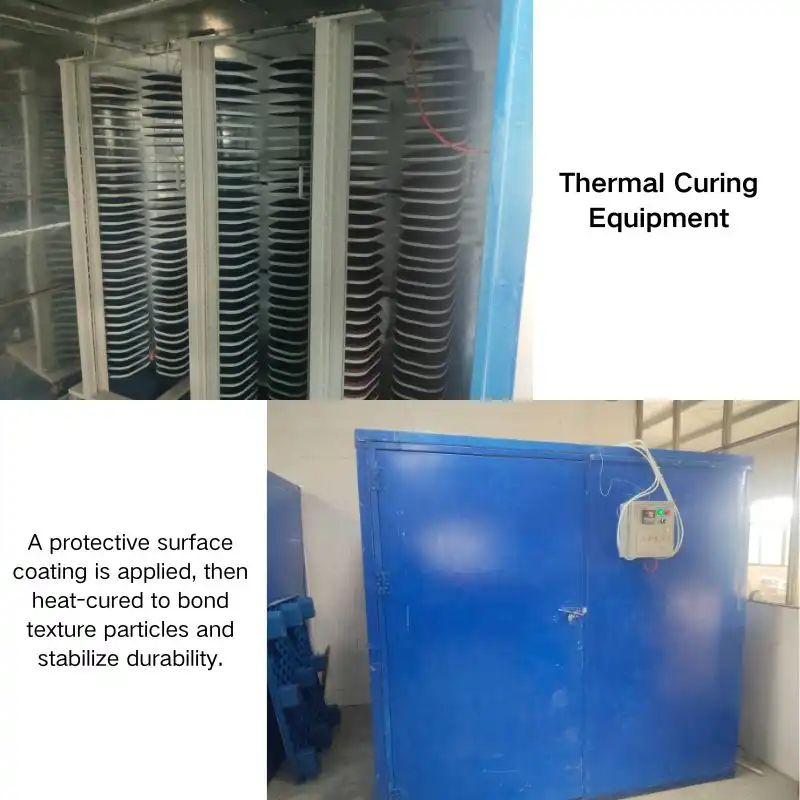
Thermal Curing Equipment
Summary for Buyers
The decision to apply Pickleball Paddle Surface Coating affects several important areas:
- Spin and ball control performance
- Protection of printed graphics
- Visual consistency across inventory
- Production cost and delivery schedules
Surface coating, often involving clear coat spray paint with texture additives, has become standard in most high-end pickleball paddle manufacturing. Buyers should evaluate their product positioning, price point, and customer expectations to determine whether this coating process aligns with their brand strategy.